D’où vont venir les matières premières pour fabriquer les batteries européennes?
Dans le monde, le marché de l’automobile évolue rapidement. La part des véhicules équipés de moteurs électriques qui est d’environ 8 % des ventes de voitures neuves en 2022 (source Agence Internationale de l'Energie, AIE) devrait passer à 35 % en 2030. En Union européenne, du fait de la règlementation interdisant les ventes de véhicules à moteur à combustion en 2035 (sauf propulsé par du e‑fuel), cette proportion passerait de 12 % à 73 % ! Les batteries des véhicules électriques sont constituées de cellules, assemblées en modules puis en packs, formant le système de batterie. La plupart des constructeurs automobiles sont intégrés jusqu'au niveau du module ou du pack, mais sous‑traitent la production de la cellule à des groupes spécialisés (Panasonic, Samsung/SDI, CATL, LG Chem, Northvolt, etc.)
Comment pourra‑t‑on produire, en Europe, plus de 15 millions de batteries dans 12 ans ?
Qui va les fournir ?
En 2020, les 5 premiers fabricants de cellules de batterie se partageaient 83 % du marché mondial (source : Goldman Sachs) et les fabricants chinois produisaient près de 60 % des batteries des voitures électriques assemblées en Europe. Ceux‑ci disposent d'un avantage en termes de coûts de fabrication de l'ordre de 20 à 25 % (grands volumes et expérience).
Quels types de technologies de batterie vont être adoptés ?
Les technologies les plus couramment adoptées sont à base de cellules Lithium‑ion et d’une anode en carbone graphite et se distinguent au niveau de la cathode :
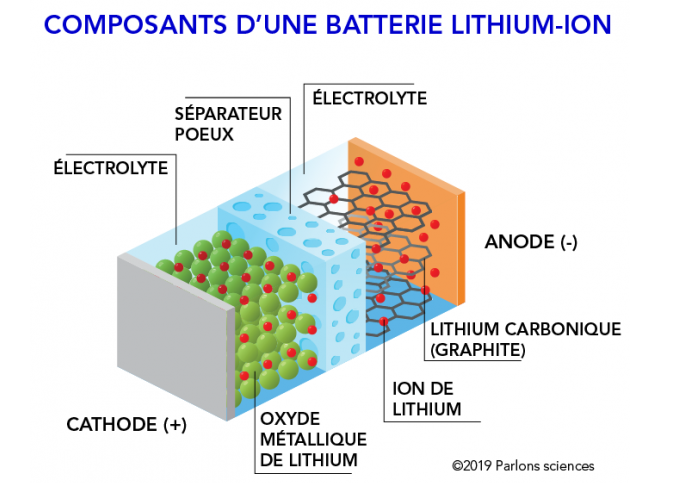
Actuellement, les constructeurs européens équipent 55 % de leurs véhicules d’une cathode NMC (Nickel Manganèse Cobalt), et 40 % d’une cathode NCA (Nickel Cobalt Aluminium) en raison de leur grande autonomie. Les cathodes LFP (5 %, Lithium Fer Phosphate) sont principalement utilisées par les constructeurs chinois qui détenaient l’exclusivité du brevet jusqu’à fin 2022. Celle‑ci est moins dense en énergie, à durée de vie plus longue et sans métaux rares. En conséquence, son coût était inférieur de 30 % en moyenne en 2021 à 135 dollars/kWh contre 185 dollars/kWh pour la NMC. Cette technologie est de plus en plus privilégiée pour les petits véhicules.
D’où vont venir les matières premières pour fabriquer les batteries ?
L'extraction et le raffinage de minéraux critiques (lithium, cobalt, manganèse, nickel, cuivre, etc.) sont pour beaucoup situés dans des pays peu exigeants sur la préservation de l’environnement et/ou des droits humains. Ainsi, 50 % des réserves mondiales de cobalt sont en République démocratique du Congo et l’exploitation du nickel entraîne de la déforestation en Indonésie. En sus, même si exploités de manière optimale, l’impact sur l’environnement reste considérable : l’exploitation du lithium en Australie, Chili, Argentine, exige de grandes quantités d’eau alors que les mines sont situées dans des zones en stress hydrique. Et la Chine contrôle 2/3 des capacités mondiales de raffinage du lithium. En outre, la méthode de production du graphite carbone la moins chère fait appel à l'acide fluorhydrique, qui est hautement toxique et corrosif, et qui nuit à l'environnement si son élimination n'est pas gérée correctement. La Chine en est le plus grand producteur.
Même si d’autres technologies émergent (ajout de manganèse dans les batteries LFMP et batteries Sodium‑Ion), la demande en minéraux devrait considérablement progresser. Selon l’AIE, les besoins en lithium d’ici 2043 vont être multipliés par 42 et ceux en nickel par 19. À horizon 2030, le déficit en lithium pourrait être de 30 %. Le recyclage pourrait améliorer la situation et le réduire à 10 %.
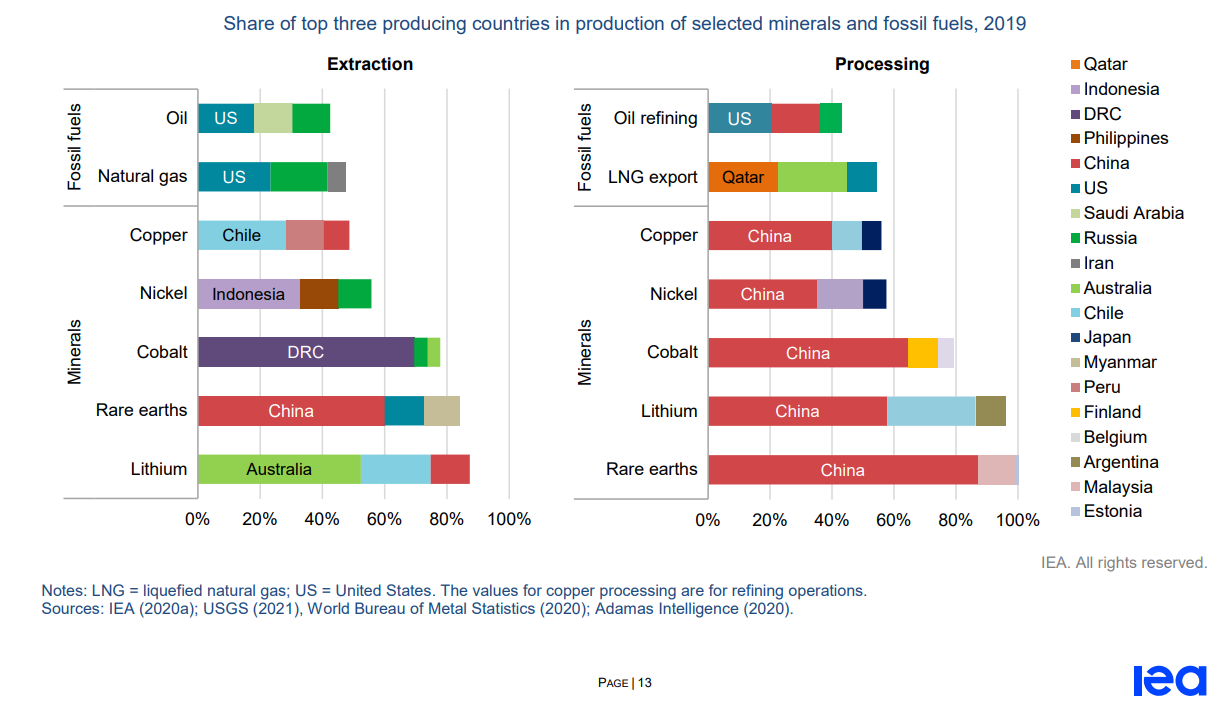
Consciente de ces déséquilibres, l’Union européenne s’est engagée à encourager les projets de construction d’usines de batteries et composants sur son territoire par l’accélération des obtentions de permis d’exploitation, l’octroi de garanties et des subventions, mais également à fixer des objectifs de recyclage et recyclabilité des batteries. On peut regretter la moindre lisibilité des incitations par rapport aux mesures mises en place aux États‑Unis dans le cadre de l’Inflation Reduction Act.
La politique européenne a été matérialisée en mars 2023 par la publication du Net Zero Industry Act et du Critical Raw Materials Act.
S’appliquant aux batteries, les mesures portent sur l’analyse du cycle de vie (2025), un diagnostic d’empreinte carbone (2024) puis exigera des niveaux maximum (2027). Ceci pourrait constituer des barrières à l’entrée pour les acteurs les moins exigeants sur les critères environnementaux. Parallèlement, les constructeurs devront récupérer à partir de 2026 une partie des matériaux composant la batterie (90 % du cobalt, nickel et cuivre et 35 % pour le lithium) et puis des niveaux supérieurs en 2035 (respectivement 95 % et 70 %). Le contenu recyclé devra augmenter à partir de 2030, de 12 % de cobalt, 85 % de plomb, 4 % de lithium et 4 % de nickel, ces niveaux passeront à 20 % de cobalt, 10 % de lithium et 12 % de nickel en 2035. Cela devant permettre à l’UE de produire elle‑même 15 % de sa consommation annuelle en 2030.
Le recyclage des batteries reste difficile en raison de leur diversité de forme et de chimie. Toutefois, l’ensemble des producteurs a lancé des tests, car il peut y avoir entre 10 % à 20 % de pertes lors de la production. Cependant, l’industrialisation pourra être lente, les batteries pouvant être utilisées dans une seconde vie pour des usages stationnaires, ceci étant finalement bénéfique pour l’environnement.
Le déficit en matières premières créé par l’essor des véhicules électriques sera partiellement compensé par les matériaux issus du recyclage des batteries. Ceci devra être complété par de nouvelles technologies de propulsion : nouvelles technologies de batterie, e‑fuel, hydrogène... ou par une plus grande utilisation des transports en commun.
Achevé de rédiger le 21 septembre 2023